The COVID-19 pandemic upended the supply chain and manufacturing leaders in the biopharma industry have spent the last few years scrambling to avoid disruptions and navigating wide swings in demand.
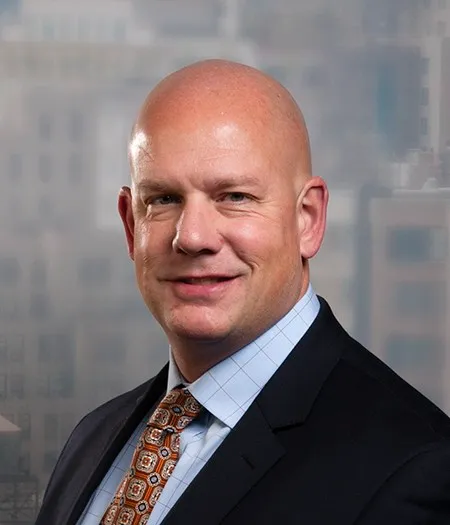
“They were really just focused on keeping the ship on a straight course and being able to maintain service levels,” said Derron Stark, EY-Parthenon managing director of strategy and transactions.
Now, new factors in the market are disrupting the normal flow of costs in manufacturing. While the supply chain situation has largely stabilized, labor costs are rising, inflation has kicked in and most companies are paying higher costs for materials than they were before the pandemic.
In fact, A late 2022 survey of pharma industry professionals conducted by GlobalData Healthcare found that 40% of respondents believed that inflation is the No. 1 challenge facing the industry in 2023.
“I think the bigger pressure, though, is on the margin side,” said Jay Welsh, EY Americas life sciences supply chain leader. “We're seeing margin pressures, which are causing manufacturing and supply chain to have to reduce their costs as opposed to avoiding added costs.”
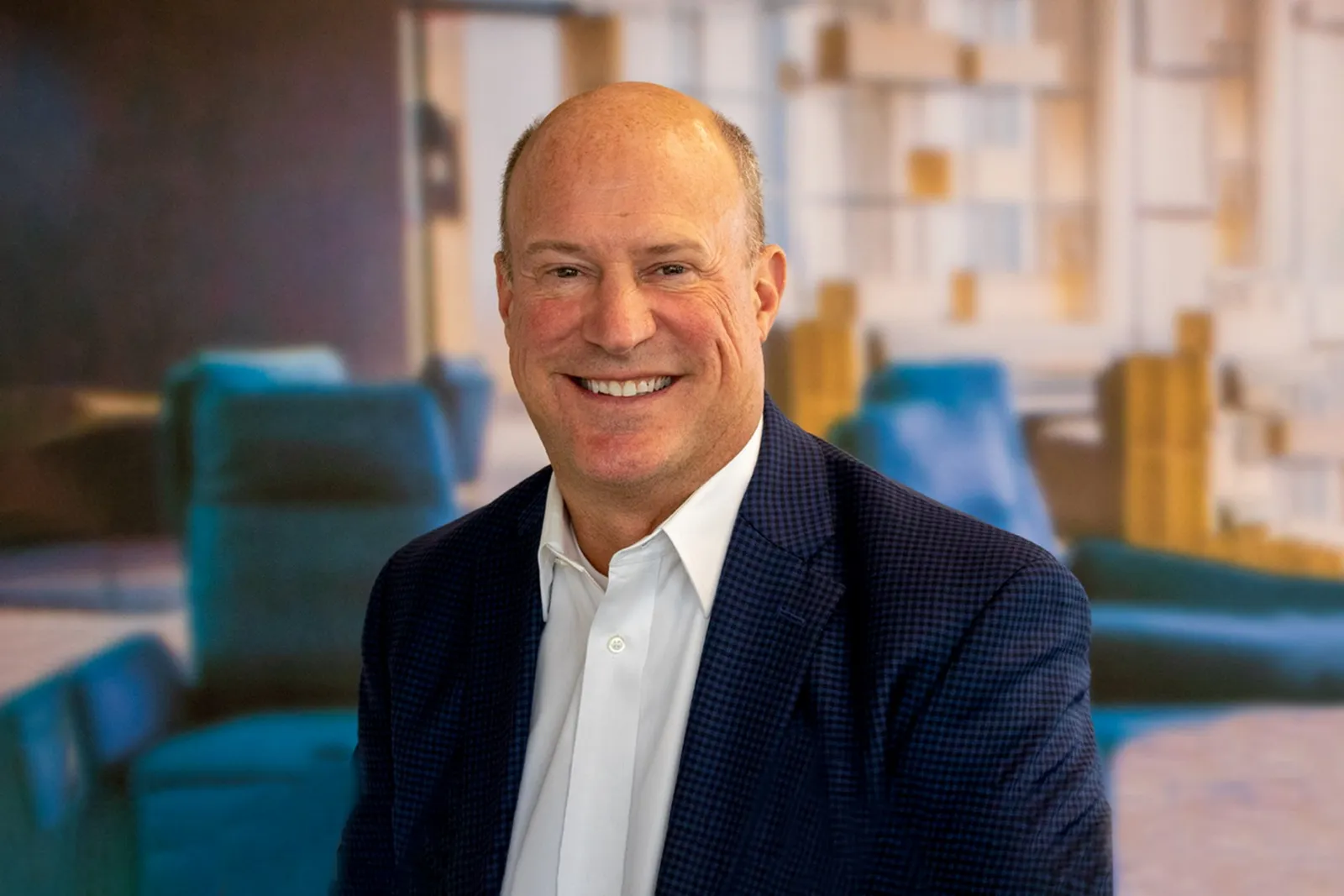
These margins are also being threatened by the major patent cliff that is looming and downward pressure on drug prices.
“Look at the recent insulin price reductions from a number of marketers of insulin. That was a massive price cut, but the cost doesn't change,” said Stark.
The Inflation Reduction Act, which contains provisions to lower prescription drug costs for Medicare patients and to reduce federal drug spending, is also having an effect.
“There's just a lot of concern that margins are going to be challenged,” said Welsh. “That's causing a lot of work and focus on cost reduction in manufacturing and supply chain.”
On top of all that, manufacturing has become more complex as advanced treatments like cell and gene therapy therapies, which require specialized processes, flood the market.
As these pressures mount, what can companies do to reign costs in?
The tech fix
“The good news is that companies and most of our clients in the biopharma space right now, in med tech as well, have opportunities for cost reduction,” Welsh said. “I think the biggest one right now is adopting digital capabilities.”
For many companies, tech solutions brought by Industry 4.0 or the Fourth Industrial Revolution have transformed manufacturing. And smart factory processes, such as AI and machine learning, which enables predictive maintenance, improvements in production yield, and autonomous planning, can help companies revamp and streamline processes. In addition, there's ever-improving software and foundational capabilities, Welsh said.
In addition, many cutting-edge manufacturing tools can also help improve planning efficiency by monitoring supply and predicting demand, which can lower costs. Manufacturing technology systems also allow companies to access troves of data that can enable a more comprehensive view of operations.
“We still don't fully know how to (cost-effectively produce) autologous or allogeneic therapies."

Derron Stark
Managing director of strategy and transactions, EY-Parthenon
“We have so much more access to data feeds from finance and operations to plant maintenance,” Stark said. “We can look at not just the operating unit, but we can look at the total cost of the facility as part of that mix across our entire product portfolio.”
Having a strong operational excellence program, a process for making an organization’s operations more efficient, is still crucial.
“Supercharging your operational excellence programs can still drive a lot of value,” Welsh said. “And we're continuing to see companies invest in that and bring a digital lens to that.”
Problem-solving is crucial
In addition to ensuring that operations run smoothly, biotech companies will also need to overcome substantial challenges to efficiently manufacture the growing number of approved cell and gene therapy products and those moving through the pipeline. Currently, nearly three dozen of these products are on the market, but more are on the way and the complexity of keeping up with manufacturing them presents a daunting challenge.
“A friend in the industry (said) their company is struggling to fully understand the value proposition of selling gene therapy products versus the cost of manufacturing,” Stark said. “We still don't fully know how to (cost-effectively produce) autologous or allogeneic therapies or do modular manufacturing at the point of administration. What is the solution to personalized therapies like cell and gene therapy, CAR-T therapies? That hasn't been solved. I think that's going to be a big challenge. But we were having the same conversations around biologics when they were being introduced because they were so expensive. The industry found a way.”
Ultimately, while the specific manufacturing challenges may have changed, the need to creatively solve problems has not.
“I think that the industry will rise to the occasion. And we consistently see (that) manufacturing, is getting better and better. From that perspective I'm very optimistic,” Welsh said.